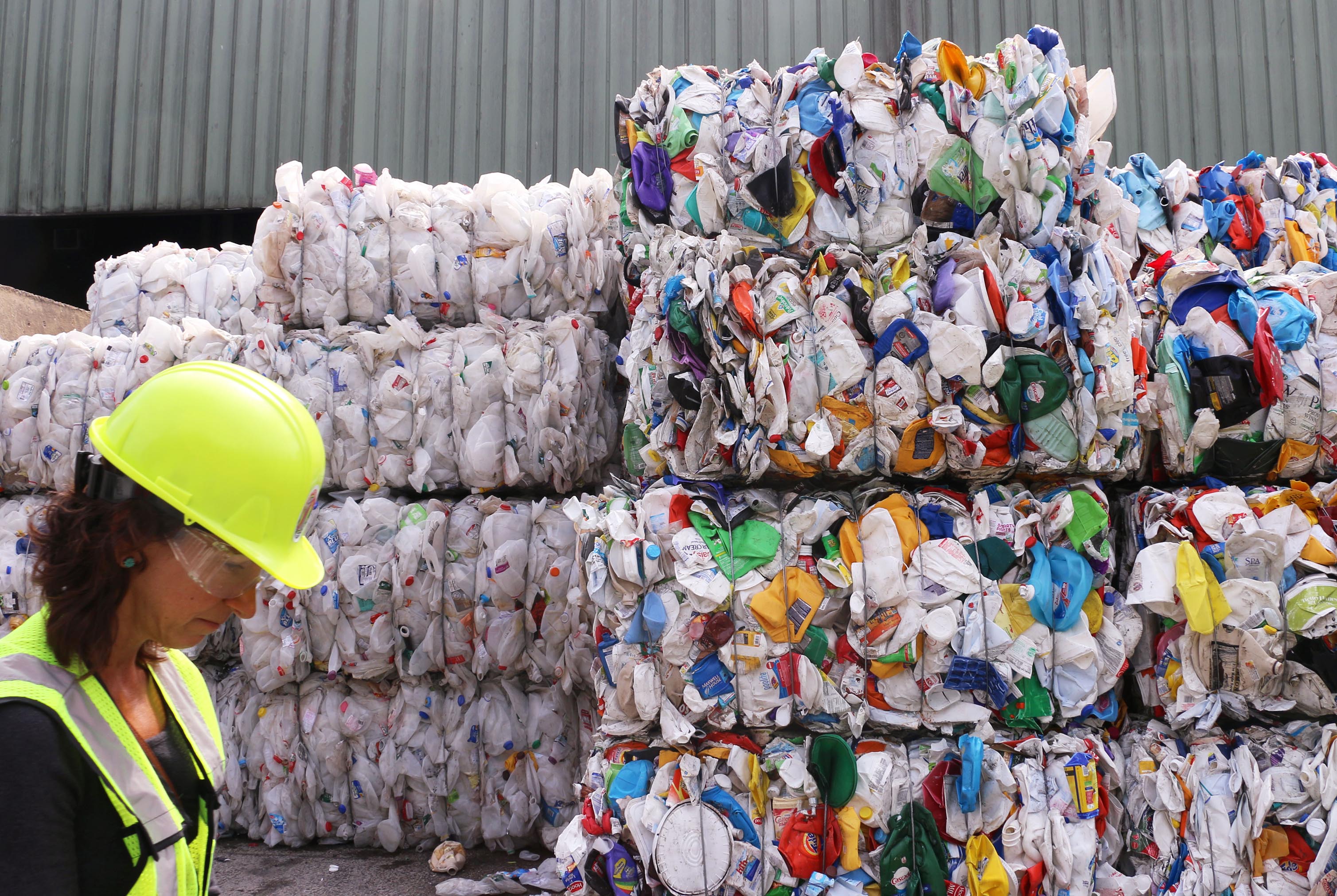
By Lorelei Poch
Environment Editor
Once Barry Von Sleet, Saint Michael’s grounds staff member, makes his run-through cleaning the grounds, you may see Casella Waste Systems pick up trash and recycling in large blue trucks, or perhaps you have visited Green Mountain Compost via an Environmental class. In either case, in order to ensure your cans do not end up smushed into the ground or the precious aluminum of which your cans are made of is not wasted by getting dumped into a landfill, understanding the process of how your recyclables are picked up, sorted, and broken down to be repurposed is crucial.
The most important thing to understand about recycling is that it is market driven, said Marketing & Communications Manager at Chittenden Solid Waste District Alise Certa . So if you recycle properly and empty and rinse your containers, MRFs (Material Recovery Facilities) will be more likely to supply buyers who manufacture repurposed items.
Know what is recyclable; since the Bottle Bills were passed statewide starting in the 1970s when hard seltzers and ciders were yet to exist, they are not included in the cans that are redeemable. So you can’t get money back for them, but you can still properly recycle them to minimize waste of such a reusable resource.
Certa emphasized that it is just as important to know what should go into your recycling bins as it is to know what goes into compost and trash. The process is complicated, however, there are simple things college students can do to help the workers at your local MRF sort the materials speeding by on the conveyor belt. Act 148 will be passed in 2020 which will make putting food scraps in the trash illegal, because identical to aluminum it is a reusable resource. According to Certa, “Not even a very small amount should be wasted.”
The process:
In the heart of Williston not far from the Burlington Airport, the beverage cans which students tossed nonchalantly over their shoulder amidst the weekend party scene enter a transformation that saves limited natural resources from being permanently extracted from the Earth.
This process can be seen through the MRF (Material Recovery Facility) Tour, a free look into what happens to your recycling after it is placed into a bin. It is here that all those recyclables that Von Sleet picked up along with the materials collected from bins on the side of streets and dumpsters from colleges get dumped on the huge concrete slab floor.
The recyclable materials start this complex journey toward reuse when they are poured onto a large conveyor belt and undergo frequent checkpoints to avoid contamination, like greasy Leonard’s pizza boxes, from continuing through the process with genuine recyclables such as White Claw Hard Seltzer cans. First the cardboard gets filtered out by large spinning rubber disks, similar to the shape of throwing stars, which, according to tour guide Lauren Layn, flick the paper goods off the belt like “licking your finger to turn a page”.
The rest of the items continue through the process where the Bottle Breaker smashes the glass products, so those green Heineken beer and cheap Barefoot rose bottles, and sends them on their own route where they are pulverized and filtered through fine then course screens. This glass, after being pulverized several times, can be repurposed as a ground layer to road construction when paving.
Meanwhile, the paper is whipped up to another conveyor belt which allows the containers to bounce down. To avoid contamination this paper and container sort process happens twice throughout the path to reuse, however, the machines can only do so much. It is ultimately the workers, like Von Sleet, who are responsible for the quality of the materials compacted and sent to manufacturers. Workers sort paper by type (such as Office Paper, Cardboard, and Newsprint/Magazine/Catalogs) and containers by composition (such as Mixed Plastic Containers, Plastic – “PET” better recognized as plastic bottles, Plastic – “HDPE” (Natural) and (Colored)) and remove contamination while an “electromagnet” attracts steel cans.
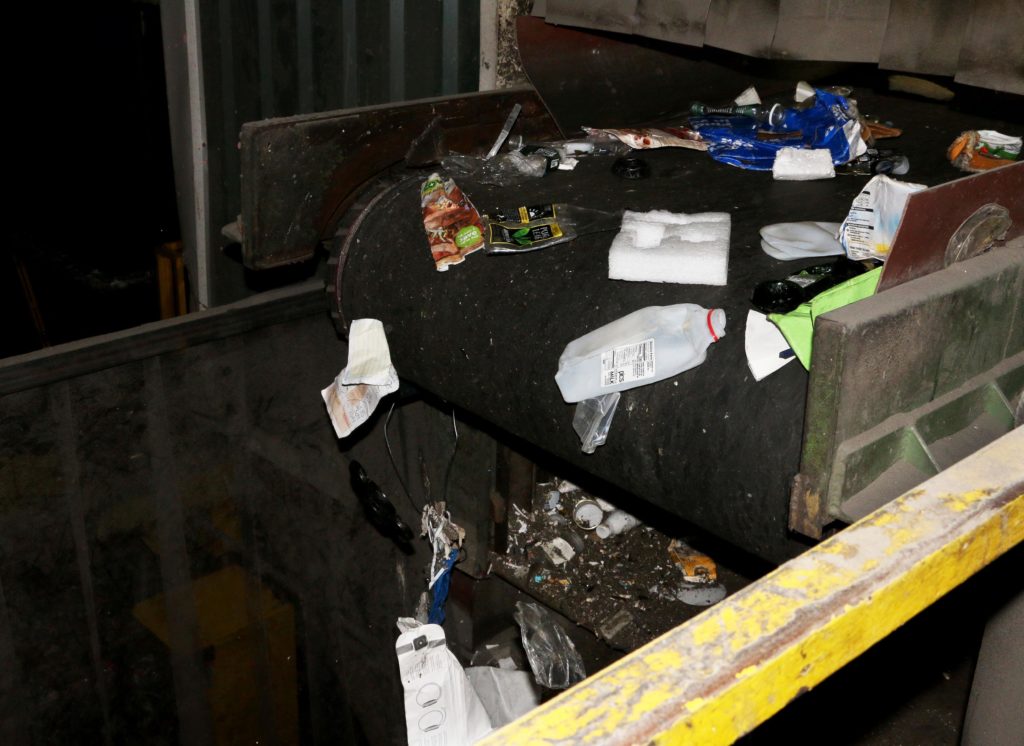
Even though there are several workers observing the conveyor belt at a time, an average of 2.5 blue bins worth of recycling travels past them each second, so contamination is inevitable. Once the workers have done their best to remove non-recyclable materials the Baler compacts the sorted materials into huge cubes ready to be picked up for resale. Recycling is market driven, so these massive blocks will remain in the MRF until manufacturers become interested in buying these materials.